Regular forklift inspections are vital for ensuring workplace safety and preventing costly accidents. The US Occupational Safety and Health Administration (OSHA) mandates daily inspections for all forklift vehicles to identify potential hazards and maintain equipment in optimal condition.
By conducting thorough inspections, businesses can extend the lifespan of their material handling equipment, reduce downtime, and avoid costly repairs. Neglecting inspections can lead to fines, equipment damage, and, most importantly, serious injuries.
This article will delve into the essential components that should be included in a comprehensive forklift inspection checklist, providing you with the tools to ensure the safety and efficiency of your operations.
Table of Contents
ToggleWhat is a Forklift?
A forklift is a specialized industrial vehicle designed to lift and move materials efficiently. It is equipped with a powered fork platform at the front, which can be raised or lowered to securely grasp and transport loads of varying sizes and weights.
Forklifts are widely used in various industries, including warehousing, manufacturing, and logistics. They are essential tools for transporting materials within and between facilities, streamlining operations, and increasing productivity.
Forklifts can be powered by either electric batteries or combustion engines, offering different performance characteristics and operating environments. Some models allow operators to sit while driving, while others require standing operation. The choice of forklift type depends on specific needs, such as load capacity, operating environment, and noise considerations.
Key Components of a Forklift
A forklift consists of several essential components working in unison to achieve its primary function of lifting and transporting materials. This machinery includes the following key components:
Chassis
The chassis, or truck frame, forms the foundation of the forklift. It houses the powertrain, steering mechanisms, and other critical components. The chassis is typically constructed of sturdy steel to withstand the rigors of industrial environments.
Counterweight
Located at the rear of the forklift, the counterweight is a heavy metal component designed to balance the load being lifted. This prevents the forklift from tipping backward, ensuring safe and stable operation.
Powertrain
The powertrain is the system responsible for generating and transmitting power to the forklift. It can be powered by:
- Internal Combustion Engines: These engines burn fuel (such as diesel, gasoline, or propane) to produce mechanical energy.
- Electric Motors: Electric motors are powered by batteries or fuel cells and offer a cleaner and quieter alternative.
Mast
The mast is the vertical structure that supports the forks and allows them to be raised and lowered. It consists of interlocking rails that provide stability and guidance. Some masts may incorporate rollers for smoother movement.
Carriage
The carriage is the horizontal component connecting the forks to the mast. It allows the forks to be moved forward and backward and tilted to accommodate different load configurations.
Industrial Applications of Forklifts
Forklifts have become indispensable tools in modern industrial operations, revolutionizing storage, shipping, and material handling. Their versatility and efficiency have made them an essential equipment for various industries.
Construction Sites
Construction sites are prime examples of environments where forklifts excel. Their ability to transport heavy materials over rough terrain and their combination of lifting and vehicle functions make them invaluable assets. Forklifts can easily unload and transport materials such as bricks, steel, and construction equipment, streamlining the construction process.
Warehouses
Warehouses are another common application for forklifts. They are used extensively for loading and unloading trucks, as well as for transporting goods within warehouse facilities. The range of forklift sizes available, from small pedestrian models to large heavy-duty trucks, accommodates diverse needs and load capacities.
Recycling Operations
Forklifts play a crucial role in recycling operations, facilitating the efficient handling of recyclable materials. They can unload recycling trucks or containers and transport the contents to sorting areas. Forklifts are also used to load and unload materials from various transportation modes, such as straight trucks, tractor-trailers, elevators, and railway cars.
Dockyards
Dockyards have long relied on forklifts for loading and unloading ships and barges. Their efficiency and versatility were particularly valuable during wartime when rapid and efficient cargo handling was essential. Today, heavy-duty forklifts transport containers between delivery trucks, dockside storage areas, and ships.
Snow Removal
In regions with heavy snowfall, forklifts can be adapted for snow removal purposes. By attaching specialized snow plow attachments, forklifts can efficiently clear snow from parking lots, sidewalks, and other areas. This provides a cost-effective alternative to traditional snow plows.
The Importance of Forklift Inspections
Forklifts are indispensable tools in industries where material handling is essential. To ensure a safe and efficient working environment, these machines must be maintained in proper operating conditions.
Regular forklift inspections are a cornerstone of safety, efficiency, and regulatory compliance. Safety regulators, forklift manufacturers, and industry experts strongly advocate for inspections to protect the well-being of employees and the integrity of equipment.
According to OSHA’s 29 CFR 1910.178 standard, forklifts must be inspected daily or after each shift in cases where vehicles are in round-the-clock use. If issues are identified during the inspection, they must be promptly reported, and the forklift must be taken out of operation until the problems are addressed. Additionally, any defects, minor or significant, should be immediately notified to the responsible party for prompt corrective action to mitigate risks.
Pre-operational inspections, conducted using a comprehensive checklist, are essential to safeguard a company’s reputation, assets, finances, and, most importantly, its employees. While establishing and maintaining an inspection routine may require initial effort, the long-term benefits in terms of safety and efficiency far outweigh the costs.
What is a Forklift Inspection Checklist?
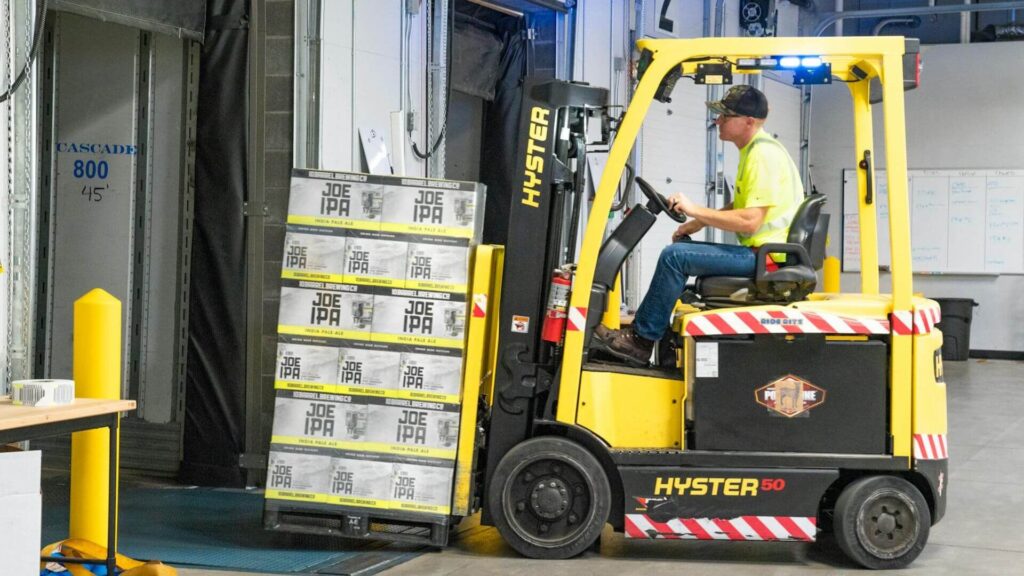
A forklift inspection checklist is a comprehensive document that outlines the specific areas of a forklift that need to be examined. It serves as a guide for operators, technicians, and safety personnel to ensure that the equipment is in good working condition.
By conducting regular inspections using a standardized checklist, businesses can identify potential hazards, prevent accidents, and minimize downtime. A well-maintained forklift operates more efficiently, reduces maintenance costs, and promotes a safer workplace.
Essential Components of a Forklift Inspection Checklist
A comprehensive forklift inspection checklist should include a thorough examination of various components, categorized into visual, operational, and additional checks. All of these components adhere to the ‘Sample Daily Checklists for Powered Industrial Trucks‘ outlined by OSHA.
Visual Checks
- Damage: Inspect the forklift for any signs of damage, such as dents, cracks, or missing parts.
- Leaks: Check for leaks of oil, hydraulic fluid, or coolant.
- Tires and Wheels: Ensure tires are properly inflated and free from excessive wear, tears, or punctures.
- Forks: Verify that the forks and locking pins are securely in place and undamaged.
- Chains, Cables, and Hoses: Inspect for any loose or damaged chains, cables, or hoses.
- Battery: Check battery charge level, condition of cables and connectors, and the presence of the battery retainer.
- Guards: Verify that all guards, including overhead protection, load backrests, gates, and side rails, are in place and undamaged.
- Mechanical Safety Devices: Inspect seat belts, fire extinguishers, nameplates, and warning labels for proper condition.
- Operator Compartment: Ensure operator controls, such as pedals and the steering tiller, are in good working order and the seat locks are properly adjusted.
Operational Checks
- Power: Verify that all indicator lights and alarms are functioning correctly, and test the power disconnect switch.
- Electrical Safety Devices: Check the horn, entry bar, audible signals, flashing lights, and indicator lights for proper operation.
- Steering: Ensure smooth steering with no binding.
- Brakes and Travel Controls: Test the foot brake pedal, braking and plugging distances, parking brake, and travel controls.
- Hydraulic Controls: Verify smooth operation of hydraulic functions and listen for any unusual noises.
- Attachments: Check the securement and proper functioning of forklift attachments, including removable parts.
- Limit Switches: Test all limit switches, including lift, tilt, travel, and safety reverse.
- Battery Charge: Ensure the battery is adequately charged before use, ideally charging it when it reaches 20-30% and allowing it to fully charge.
- Wire Guidance (if applicable): Verify the proper functioning of wire guidance systems.
- End Aisle Control: Check that the forklift slows down and stops at the aisle end as expected and that the alarm functions correctly.
Additional Checks
- Labels and Markings: Verify the presence and readability of nameplates, labels, and markings.
- Exhaust System: Inspect the exhaust system for sparks or flames.
- Cleanliness: Ensure the forklift is clean and free from dirt, excess oil, or grease.
- Propane Tank (if applicable): Inspect the propane tank for rust or corrosion.
- Operator’s Manual: Verify the presence of the operator’s manual.
- Seatbelt: Check the proper functioning of the seatbelt.
- Capacity Load Plate: Ensure the capacity load plate is securely attached.
- Gas Levels (for gas-operated forklifts): Verify sufficient gas levels before operating the forklift.
- Horn and Reverse Buzzer: Check the proper functioning of the horn and reverse buzzer.
How to Create a Forklift Inspection Checklist?
Developing a comprehensive forklift inspection checklist is essential for ensuring the safety and efficiency of your operations. By following these guidelines, you can create a customized checklist that aligns with your specific needs and regulatory requirements.
- Identify Critical Components: Begin by identifying the key components of a forklift that require regular inspection. These components typically include tires, brakes, steering, mast, hydraulics, electrical systems, forks, and attachments.
- Define Inspection Procedures: Outline the specific procedures for inspecting each component. This may involve visual checks, functional tests, or measurements. For example, tire inspections should include checking tire pressure, tread depth, and signs of damage.
- Determine Inspection Frequency: Establish a clear inspection schedule based on factors such as the intensity of forklift usage, industry regulations, and company policies. Daily inspections may be required for frequently used forklifts, while weekly or monthly inspections might suffice for less intensive use.
- Create a Checklist Format: Design a clear and organized checklist format that is easy for operators to follow. Consider using a digital checklist or a paper-based template. Include sections for recording inspection results, identifying defects, and tracking corrective actions.
- Train Operators: Provide comprehensive training to operators on the proper use of the inspection checklist and the importance of conducting thorough inspections. Ensure that operators understand the procedures for reporting defects and taking corrective actions.
- Review and Update Regularly: Periodically review the checklist to ensure it remains accurate and relevant. Update the checklist as needed to reflect changes in forklift models, industry regulations, or company policies.
Forklift Inspection Best Practices
Effective forklift inspection practices are essential for ensuring the safety and efficiency of your operations. By following these guidelines, you can optimize your inspection process and minimize the risk of accidents and equipment failures.
- Conduct Thorough Inspections: Ensure that inspections are comprehensive and cover all critical components of the forklift. Follow a standardized checklist to ensure consistency and thoroughness.
- Train Operators: Provide operators with comprehensive training on forklift inspection procedures, including the use of checklists, identification of defects, and reporting requirements.
- Document Inspection Results: Maintain detailed records of inspection results, including any defects identified and corrective actions taken. This documentation can be used for compliance purposes and to track the overall condition of your forklift fleet.
- Prioritize Safety: Always prioritize safety during inspections. If a critical defect is identified, take immediate action to address the issue and remove the forklift from service until it is repaired.
- Address Defects Promptly: Ensure that any defects identified during inspections are promptly addressed to prevent further damage or accidents. Implement a system for tracking and resolving defects in a timely manner.
- Conduct Regular Maintenance: In addition to inspections, schedule regular maintenance for your forklifts to address potential issues before they become problems. This can include oil changes, filter replacements, and other routine maintenance tasks.
- Use a Standardized Checklist: Employ a standardized inspection checklist that is tailored to your specific forklift models and industry regulations. This will ensure consistency and help identify potential safety hazards.
- Involve Operators: Encourage operators to participate in inspections and report any issues they observe. This can help identify problems early and promote a culture of safety.
- Review and Update Checklist: Periodically review and update your inspection checklist to ensure it remains accurate and relevant. Consider incorporating changes based on new regulations, industry best practices, or changes in your forklift fleet.
- Consider External Inspections: In addition to internal inspections, consider engaging an external inspection service to provide an independent assessment of your forklift fleet. This can help identify potential issues that may be overlooked during internal inspections.
Frequently Asked Questions (FAQs)
Q1: What is the minimum frequency for forklift inspections?
While OSHA mandates daily inspections, the optimal frequency may vary depending on factors such as the intensity of forklift usage, industry regulations, and company policies. Some organizations may require more frequent inspections, especially for critical applications or in hazardous environments.
Q2: Can I use a generic forklift inspection checklist for all my vehicles?
While a generic checklist can provide a solid foundation, it’s essential to customize it to your specific forklift models, attachments, and operating conditions. Consider factors such as the type of power source (electric, diesel, propane), load capacity, and any unique features of your vehicles.
Q3: How can I ensure that operators are following the inspection procedures?
Implement a system of accountability, such as requiring operators to sign off on completed checklists. Consider providing regular training on the importance of inspections and the consequences of non-compliance. You may also want to conduct random audits to verify compliance.
Q4: What should I do if a defect is identified during an inspection?
If a defect is found, immediately remove the forklift from service and report the issue to the appropriate personnel. Implement a system for tracking and addressing defects promptly. Ensure that necessary repairs are made before the forklift is returned to service.
Q5: How can I integrate forklift inspections into my overall safety management system?
Forklift inspections should be a part of your broader safety management system. Develop clear procedures for conducting inspections, reporting defects, and taking corrective actions. Consider using software or digital tools to streamline the inspection process and track compliance.
Q6: What are the potential consequences of neglecting forklift inspections?
Failure to conduct regular forklift inspections can lead to a variety of negative consequences, including:
- Accidents and injuries: Defective forklifts can pose serious safety risks to operators and other workers.
- Equipment damage: Neglecting maintenance can lead to equipment failures and costly repairs.
- Downtime: Faulty forklifts can disrupt operations and reduce productivity.
- Regulatory violations: Non-compliance with OSHA regulations can result in fines and penalties.
- Damage to reputation: Safety incidents can tarnish a company’s reputation.
Conclusion
A comprehensive forklift inspection checklist is a vital tool for ensuring the safety, efficiency, and compliance of your forklift operations. By following the guidelines outlined in this article, you can create a customized checklist that aligns with your specific needs and regulatory requirements.
Regular inspections are essential for identifying potential hazards, preventing accidents, and minimizing downtime. By prioritizing safety and conducting thorough inspections, you can contribute to a safer and more productive workplace.
Here are some next steps that you can do:
- Create Your Checklist: Use the information provided in this article to develop a tailored forklift inspection checklist that addresses your specific needs.
- Train Your Operators: Ensure that your operators are trained on the proper use of the checklist and the importance of conducting thorough inspections.
- Implement a Routine: Establish a regular inspection schedule and integrate inspections into your overall safety management system.
- Monitor and Improve: Continuously review and update your checklist to ensure it remains effective and aligned with industry best practices.
By taking these steps, you can significantly enhance the safety and efficiency of your forklift operations.
Streamline Forklift Inspections with DATAMYTE
DATAMYTE is a quality management platform with low-code capabilities. Our Digital Clipboard, in particular, is a low-code workflow automation software that features a workflow, checklist, and smart form builder. This tool lets you create and implement custom forklift inspection checklists to ensure consistent and thorough evaluations, reducing the risk of missed steps and enhancing safety.
DATAMYTE also lets you conduct layered process audits (LPA), a high-frequency evaluation of critical process steps, focusing on areas with the highest failure risk or non-compliance. Conducting LPA with DATAMYTE lets you effectively identify and correct potential defects before they become major quality issues.
With DATAMYTE, you have an all-in-one solution for automating and optimizing your forklift inspection processes, ensuring compliance, safety, and efficiency. Book a demo now to learn more.